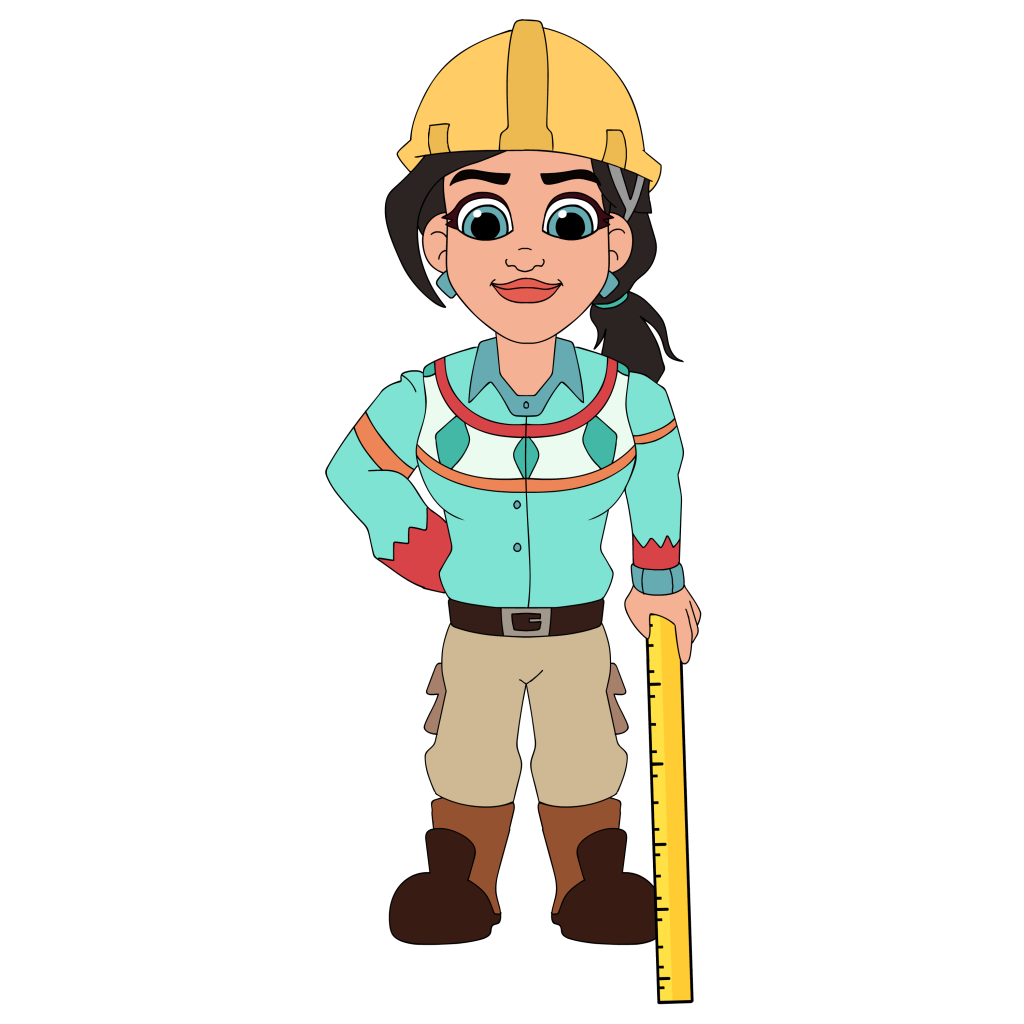
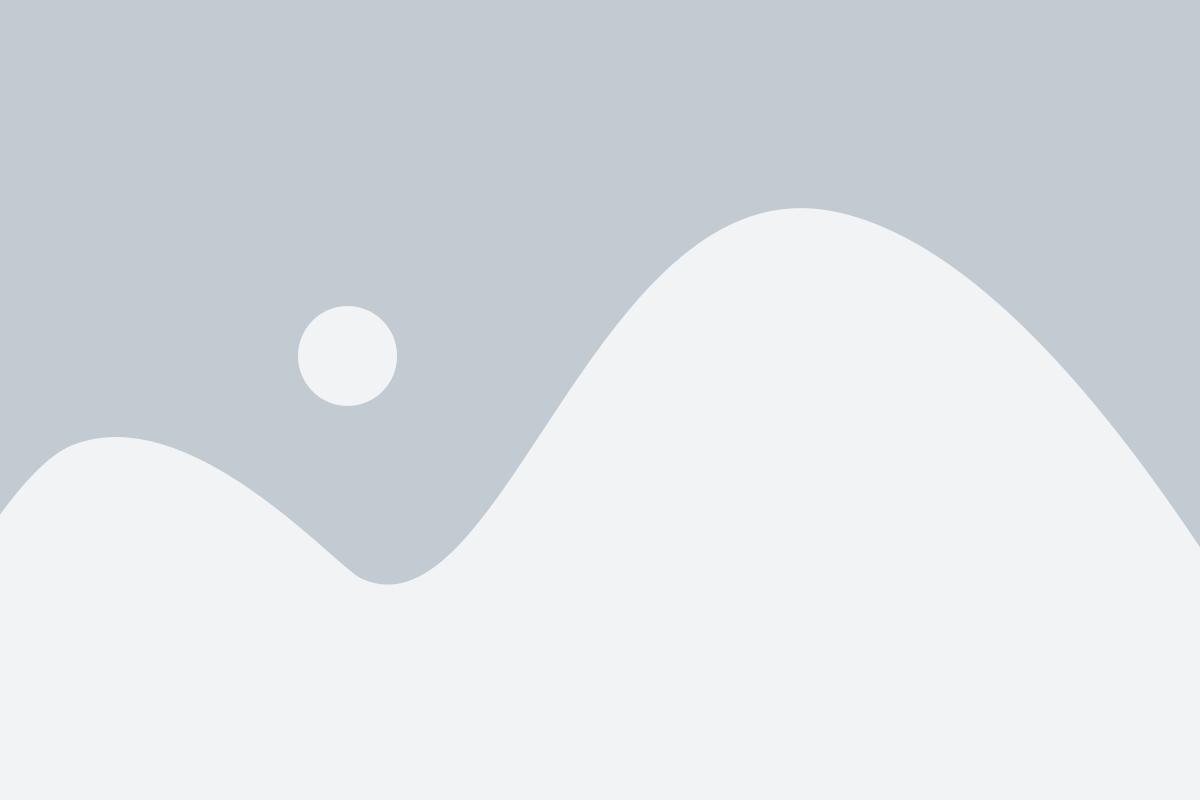
Parts Get Pulled, But Never Logged
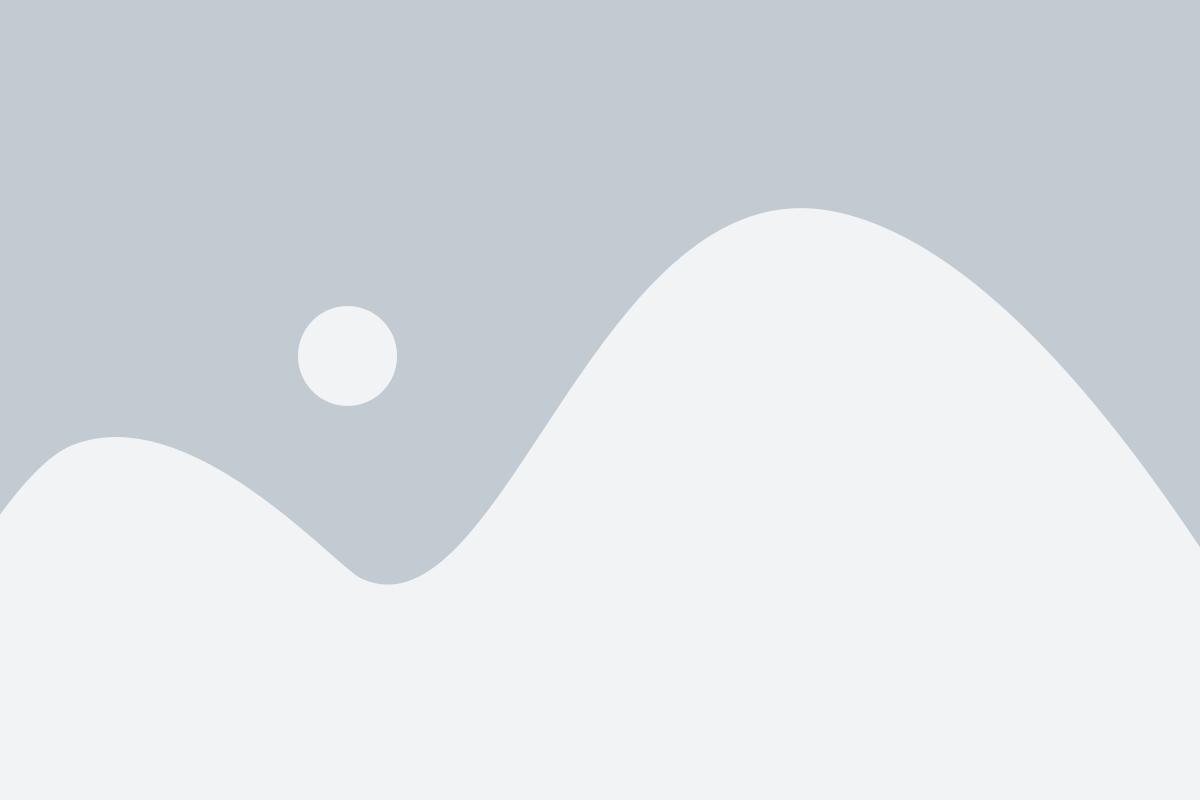
Repairs Happen, but Budgets Don’t Reflect It
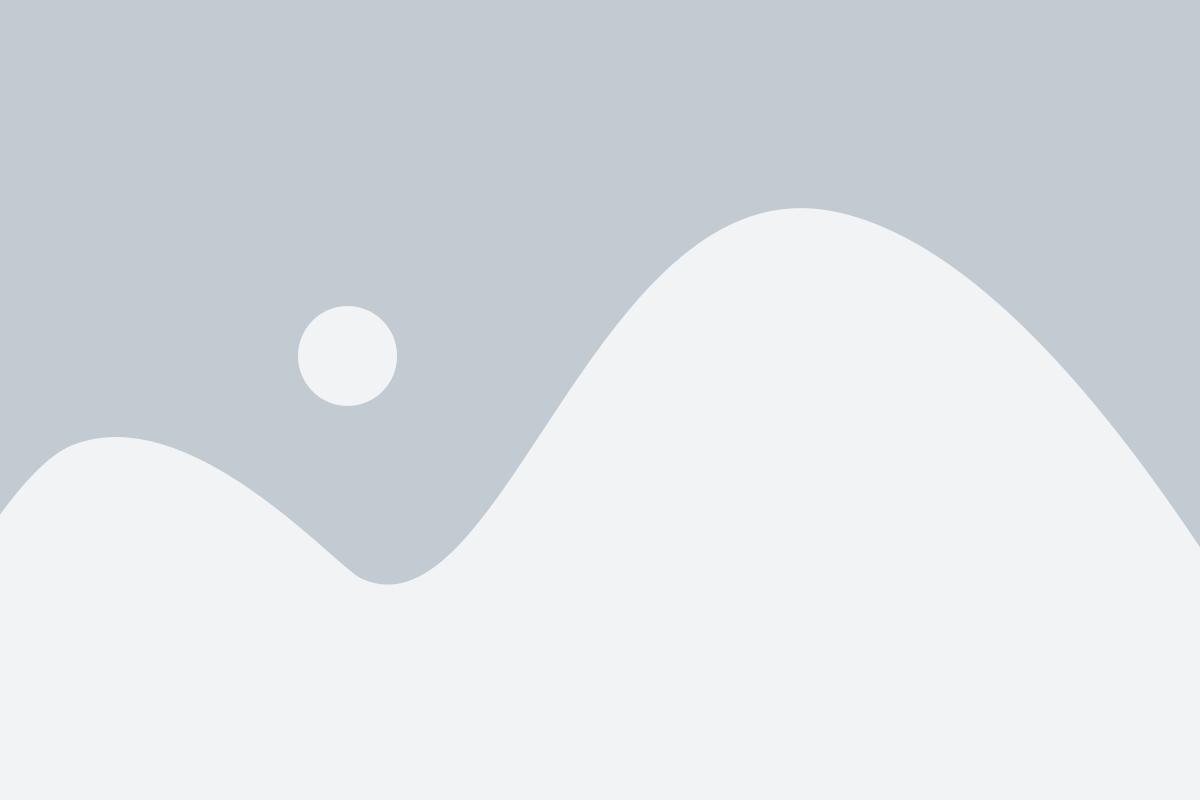
Usage Lives Outside the Job System
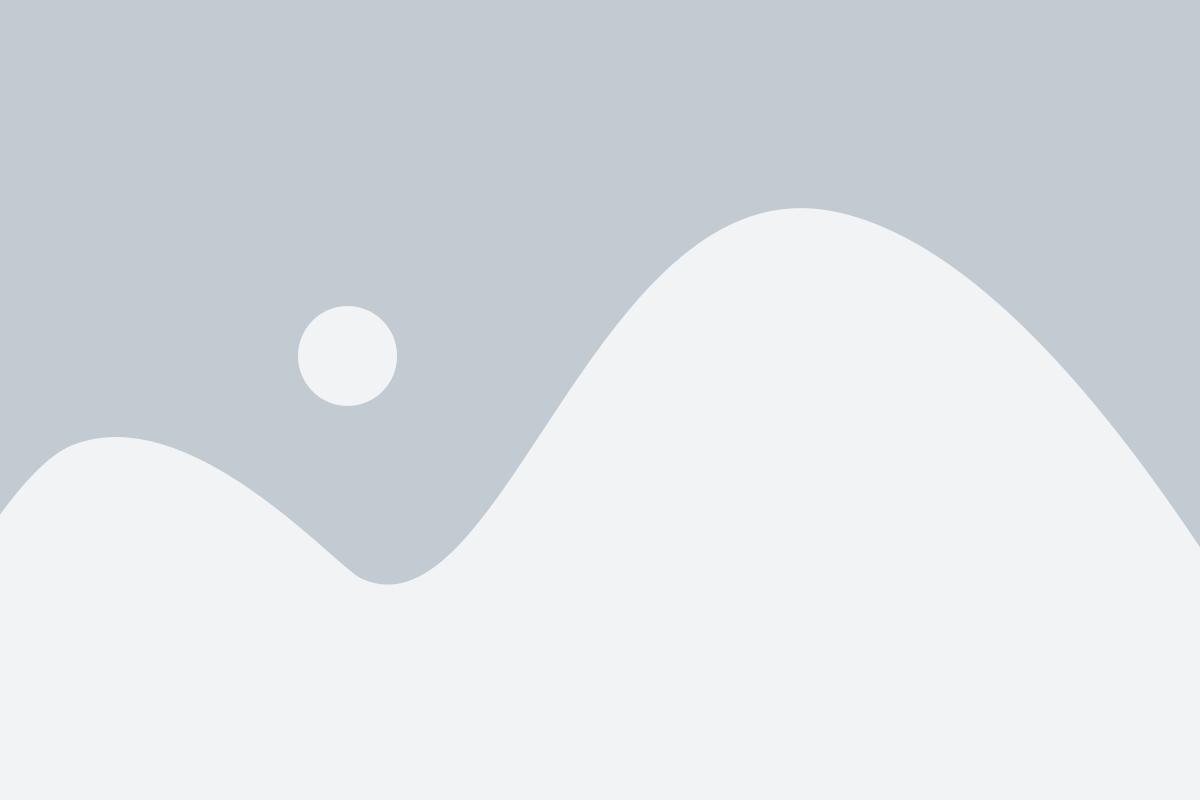
Stockouts and Overstocking—Both at Once
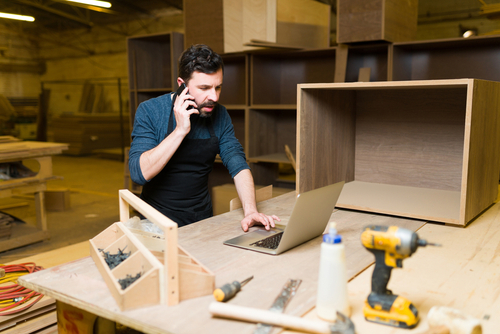
Spare Parts Usage – Know What Was Used, Where, and Why
Track every spare part consumed during maintenance, repair, or replacement. The Spare Parts Usage app connects inventory with operational activity — ensuring accurate stock levels, cost tracking, and asset service history.
System Preview
Why Woodshop Master?
Connect Inventory to Maintenance
Job-Linked Parts, Logged in Real Time
Ensure every bolt, filter, and fuse has a traceable record — no more mystery usage or stock drift.
Real-Time Part Usage Logging
Live Inventory Deduction
Linked to Work Orders & Assets
Tracks Failure & Job Context
Supports Reorder Planning
Cost Attribution by Asset or Job
Integrated Apps
Spare Parts Usage integrates with:
Asset Master Records
Work Order Management
Maintenance Scheduling For Assets
Inventory Control
Stock Transfers
Failure Mode Analysis
Audit Trail
App Features
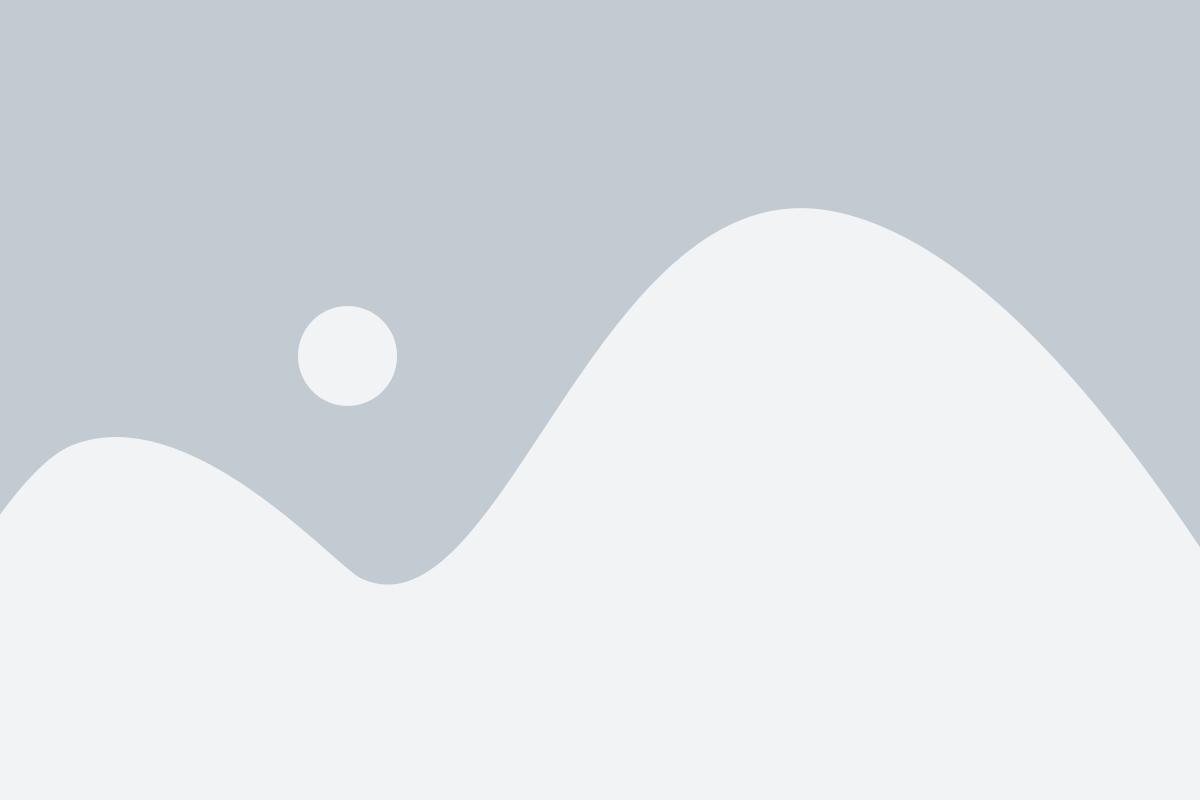
Usage Tracking at Job & Asset Level
Log every part used per job — including quantity, location, technician, and reason for use.
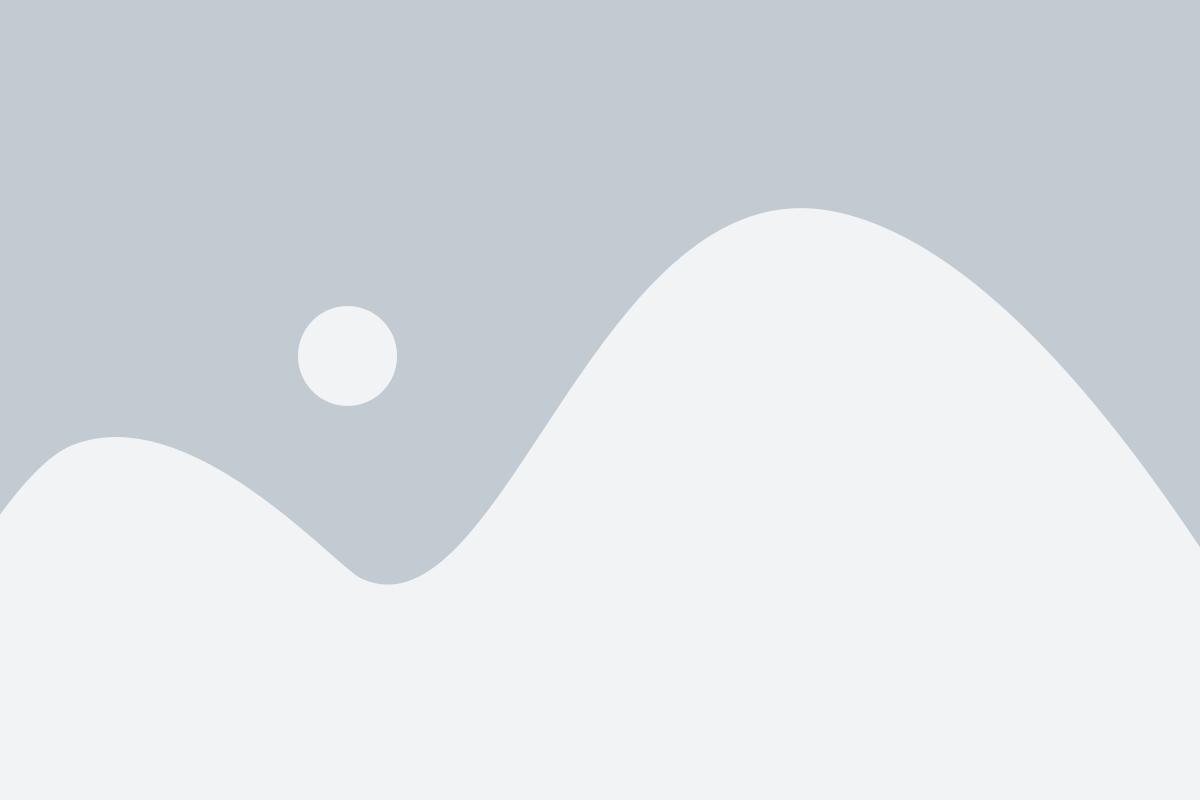
Live Inventory Deduction
As parts are logged against a work order, inventory is instantly updated to reflect consumption.
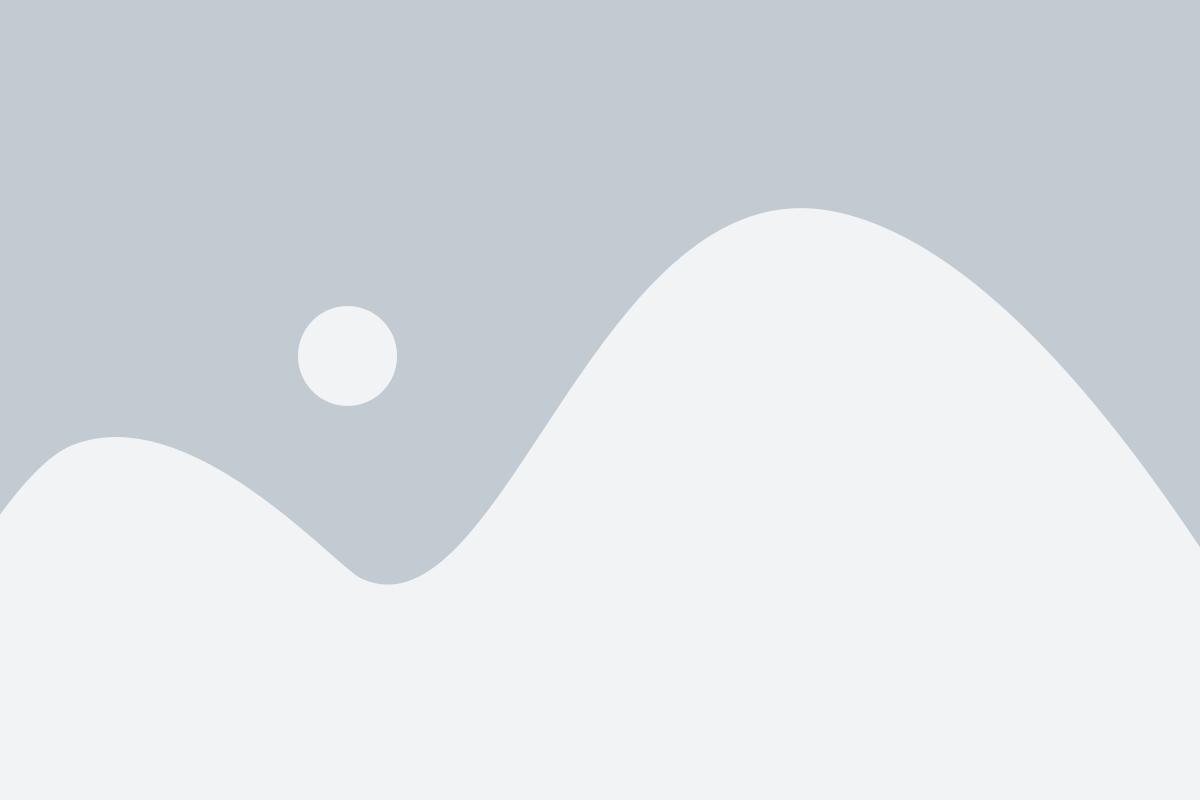
Failure Mode & Cause Linkage
Tag parts used to specific failure codes or issues — and spot recurring problems.
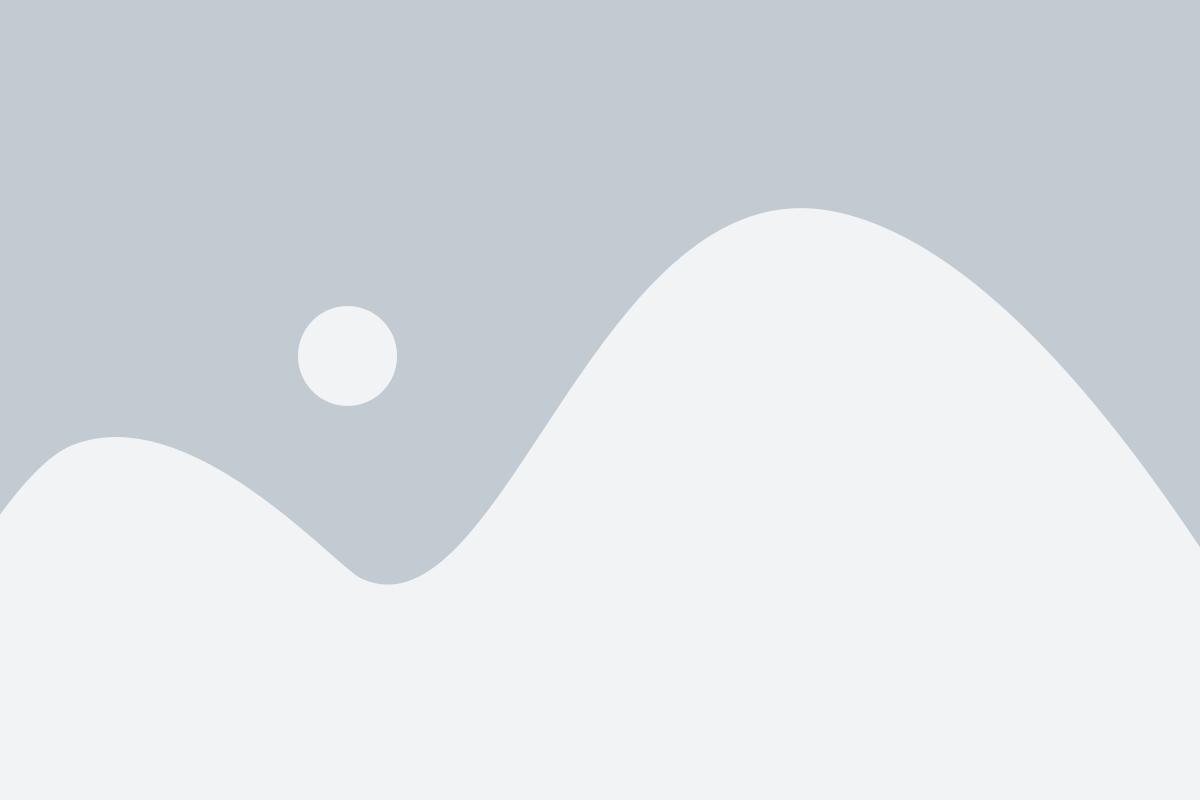
Cost Attribution by Context
Know what each repair costs — not just in labor, but in materials too. Attribute part cost to assets, teams, or service requests.
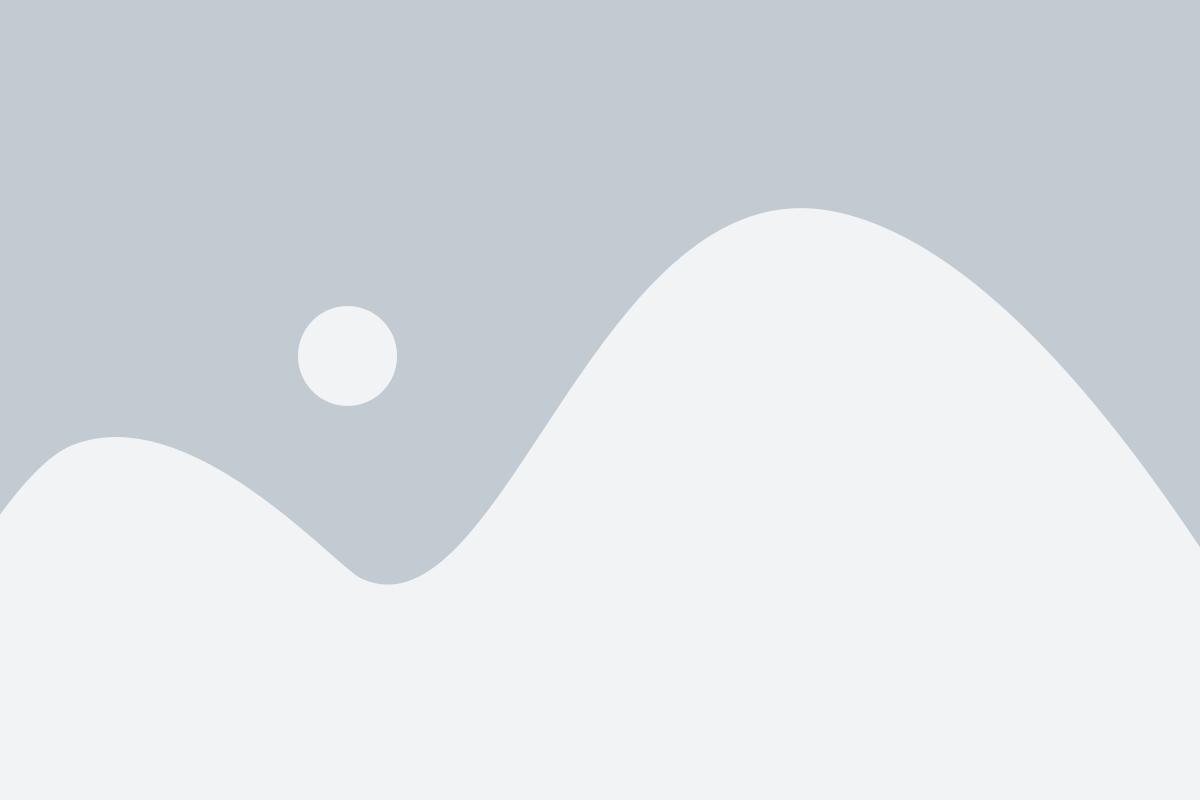
Alerts for Unusual Usage
Get flagged when parts are consumed outside expected patterns — helping prevent theft or misdiagnosis.
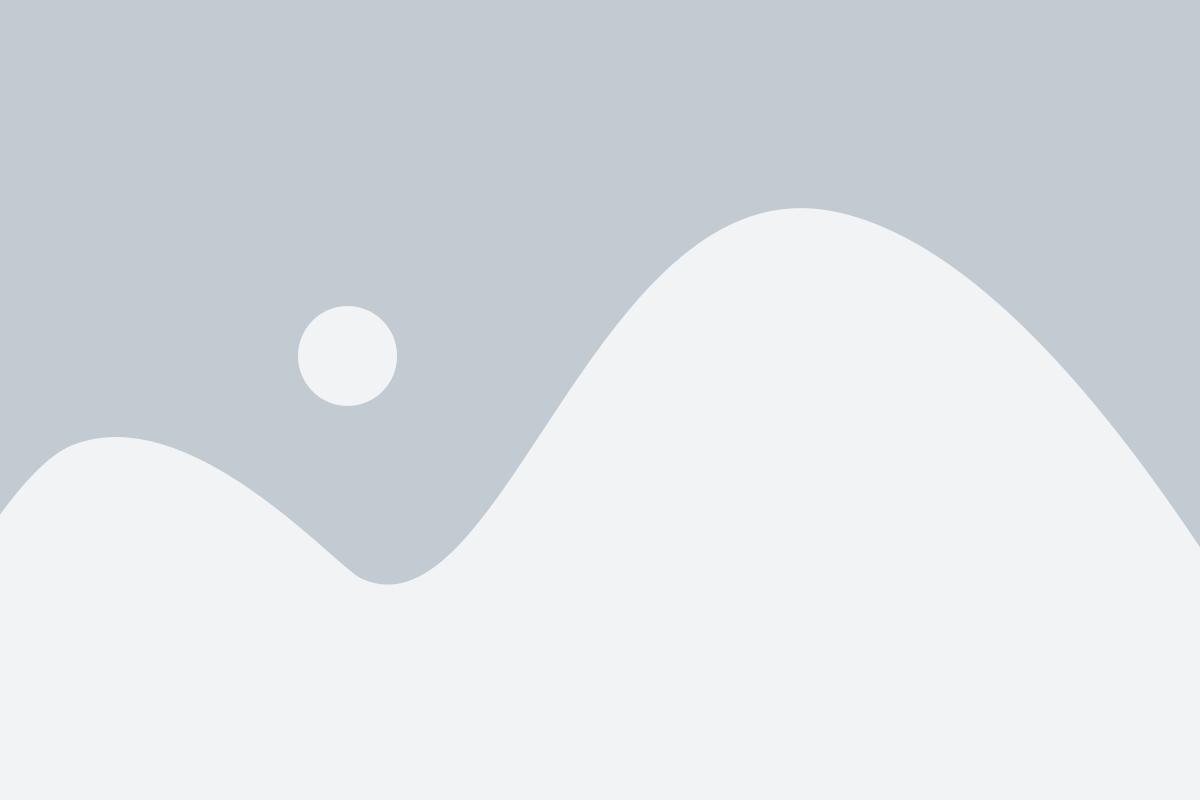
Full Usage History
Review every instance a part was used — across all assets, jobs, and locations.
See It in Action
Stop guessing. Start logging.
Track every part — and make every repair smarter.