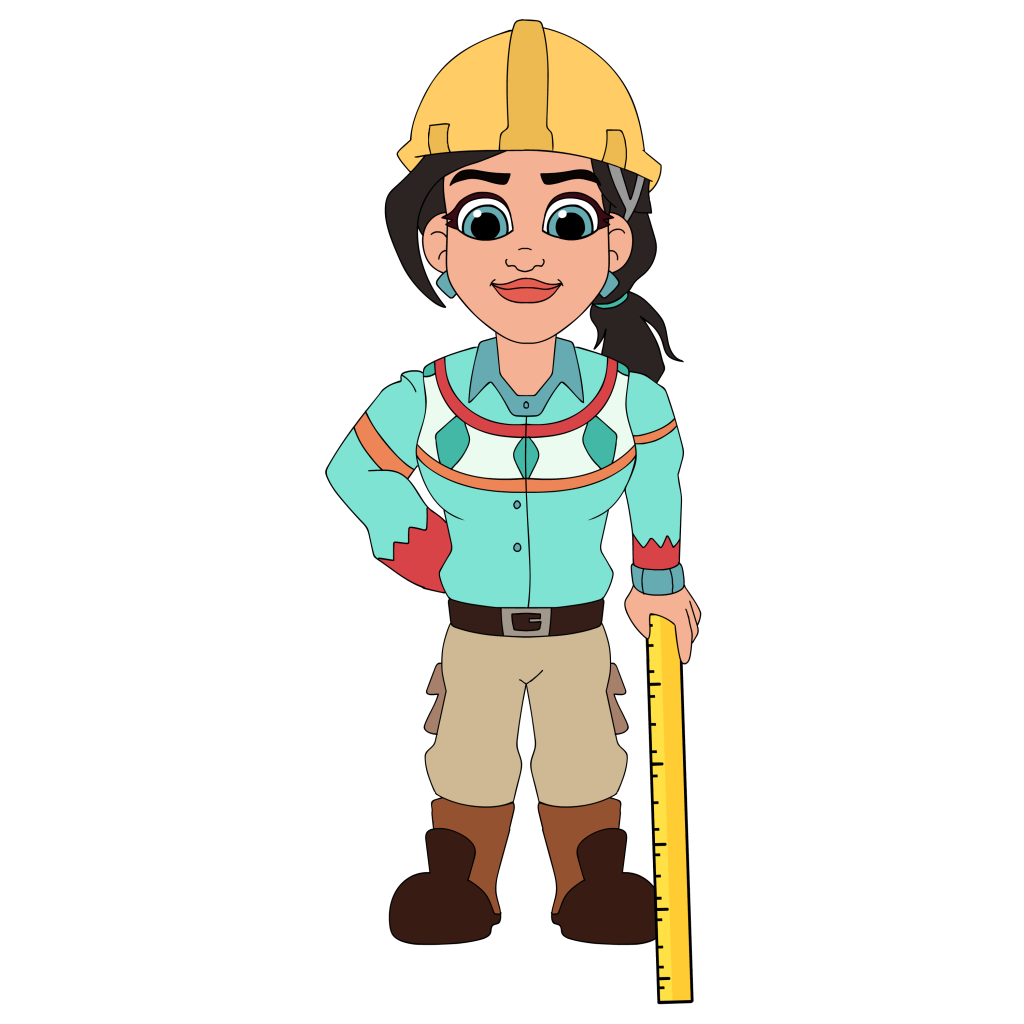
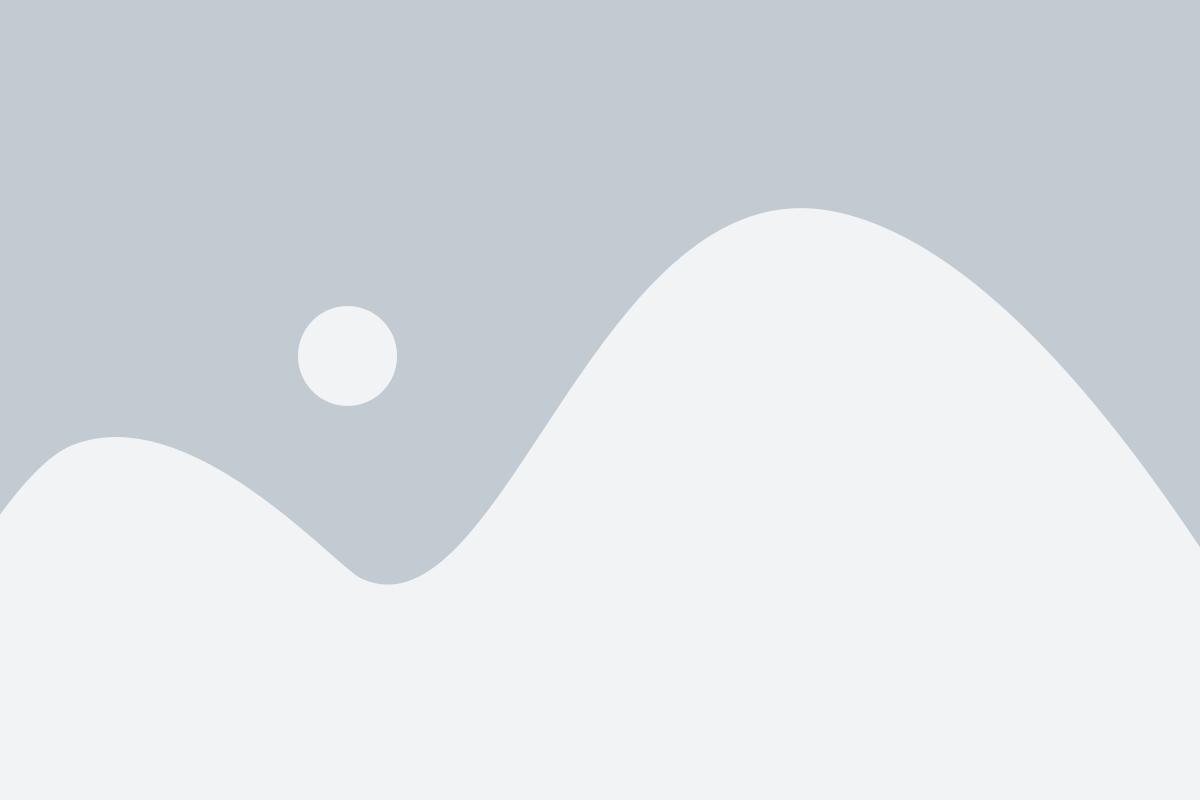
Missed Opportunities to Improve
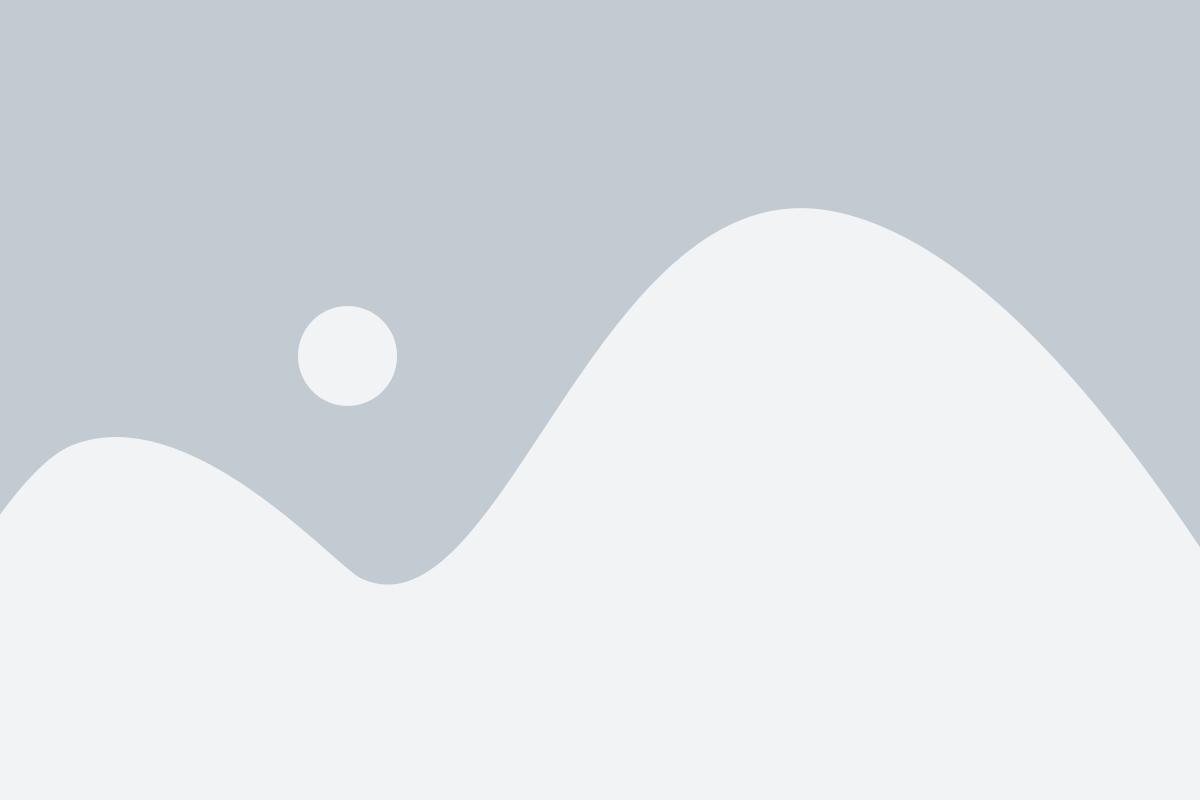
Same Issues, No Solutions
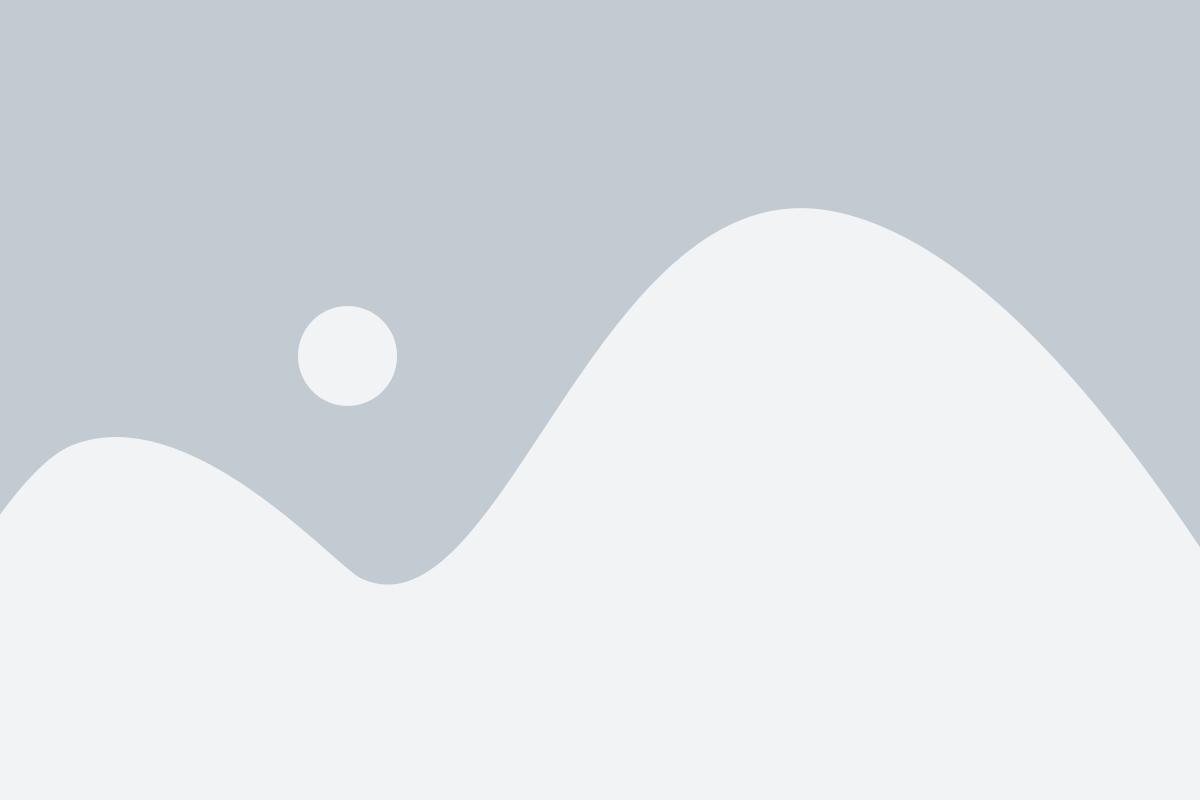
Events Fall Through the Cracks
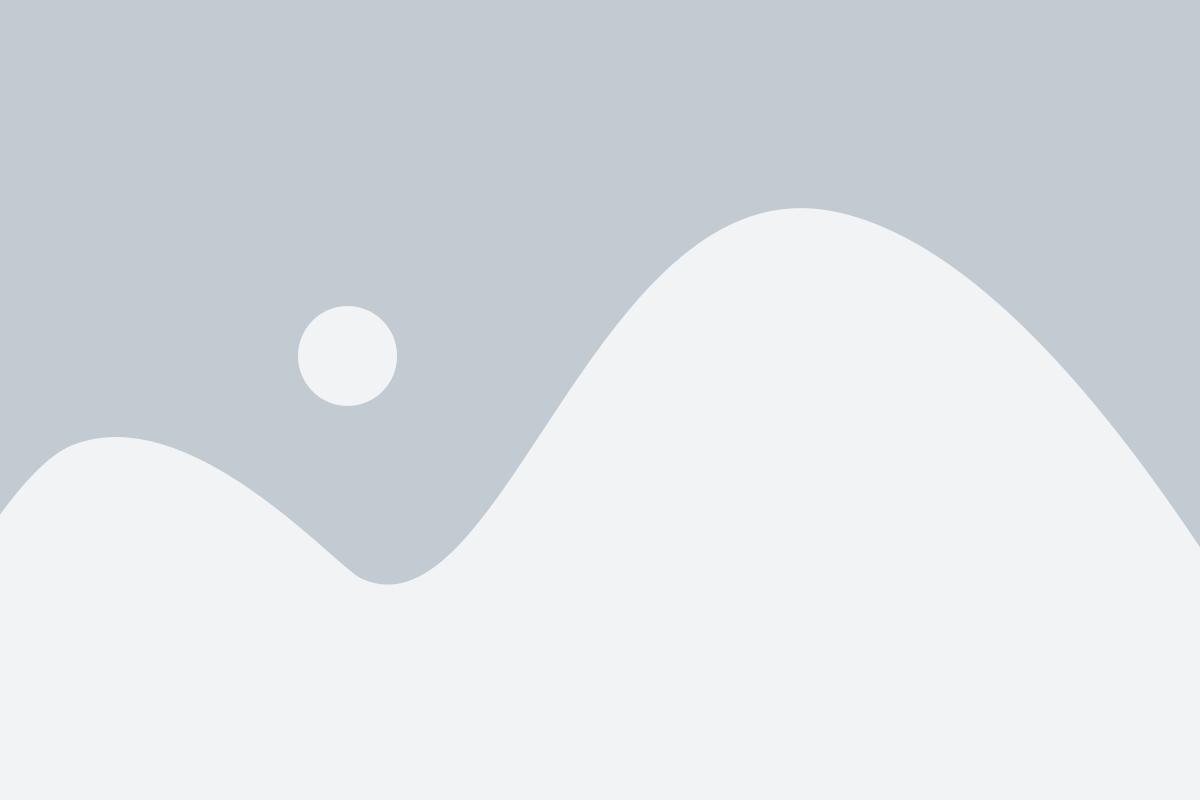
Downtime Data Stays in a Silo
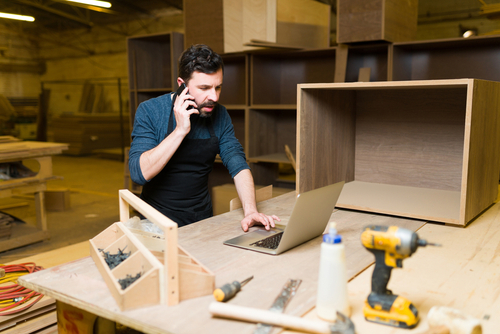
Downtime Logs – Capture Every Minute That Equipment Stands Still
Log, categorize, and analyze unplanned and scheduled downtime in real time. The Downtime Logs app transforms idle time into actionable insight — helping you reduce interruptions, flag failure trends, and keep operations flowing
System Preview
Why Woodshop Master?
Log It. Learn From It. Improve It.
Every Delay, Fully Documented
Capture duration, root cause, and impact in one log — linked to your equipment and service records.
Real-Time Downtime Capture
Root Cause Visibility
Tied to Asset & Work Orders
Filters by Line, Location, or Reason
Dashboards & Exportable Reports
Integrated With Maintenance Logic
Integrated Apps
Downtime Logs integrates with:
Asset Master Records
Maintenance Scheduling For Assets
Failure Mode Analysis
Work Order Management
Total Cost of Ownership (TCO)
Audit Trail
App Features
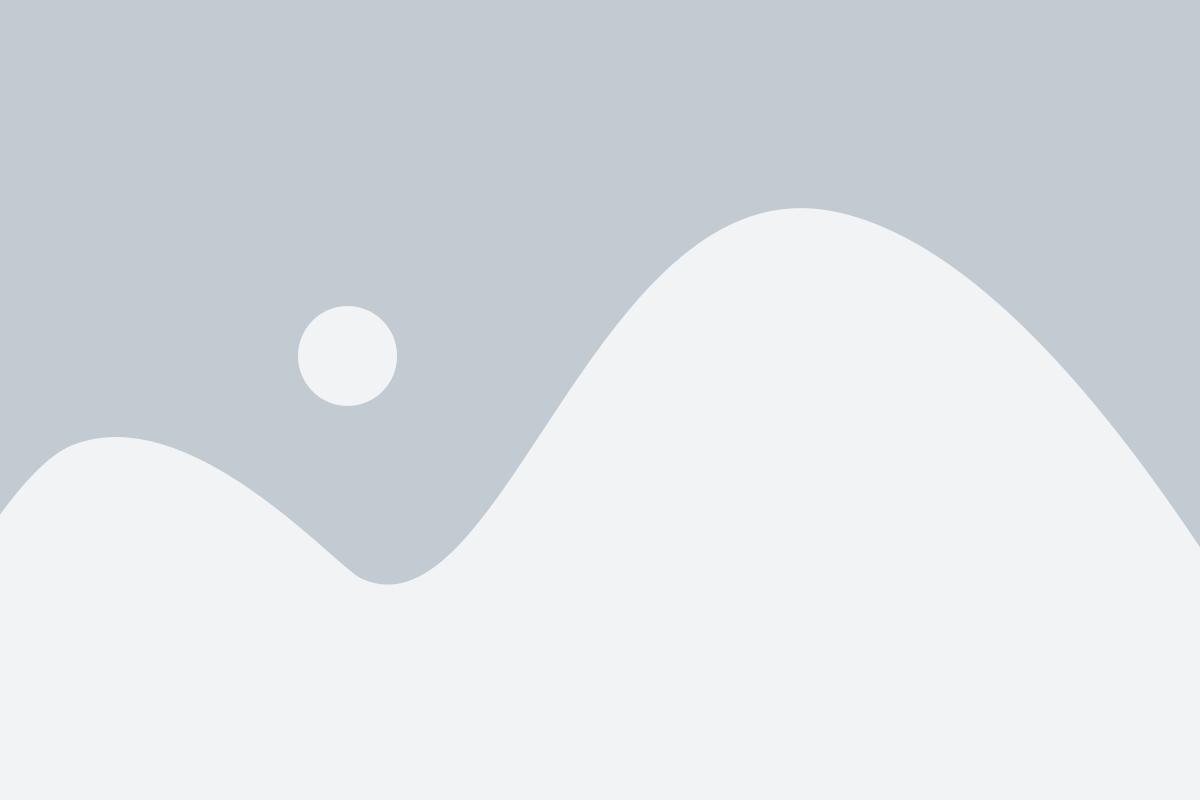
Live Downtime Entry with Start/Stop Controls
Technicians and operators can log downtime in real time — ensuring duration accuracy and event traceability.
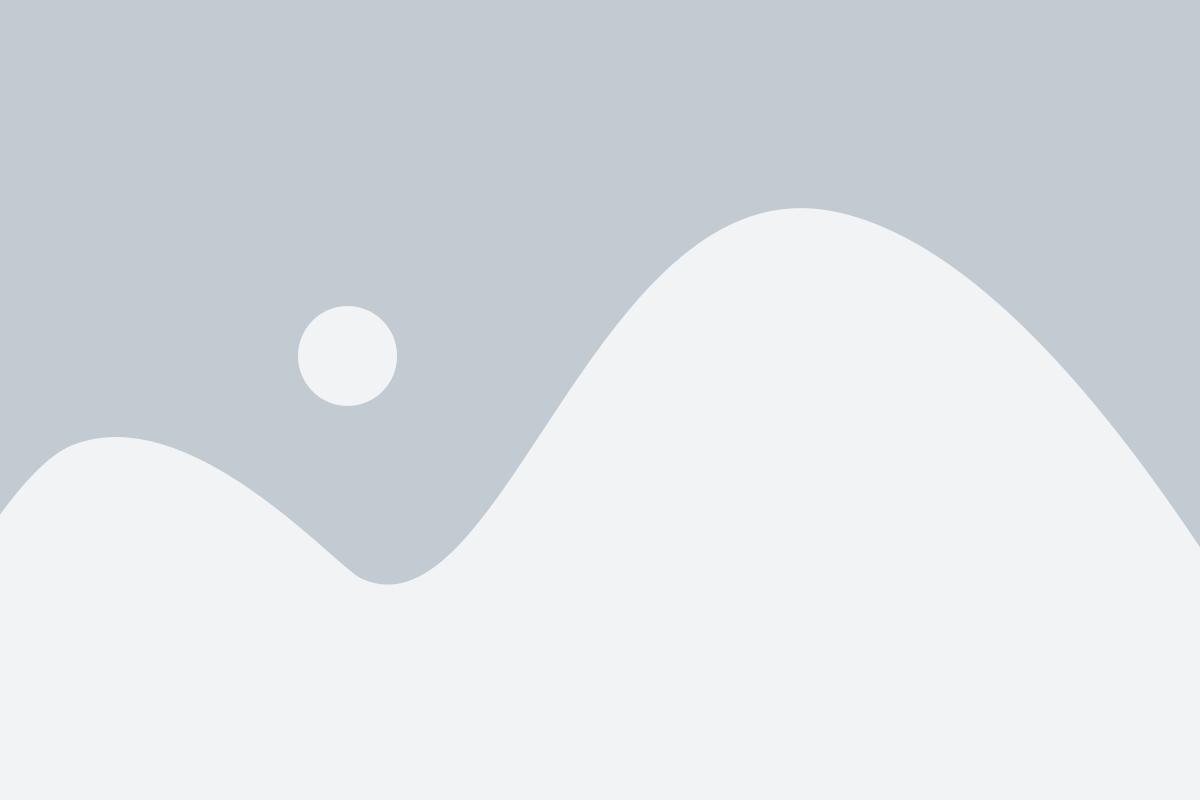
Cause & Impact Classification
Categorize downtime by origin (internal vs external, mechanical vs human) and tag resulting impacts (e.g., missed production targets).
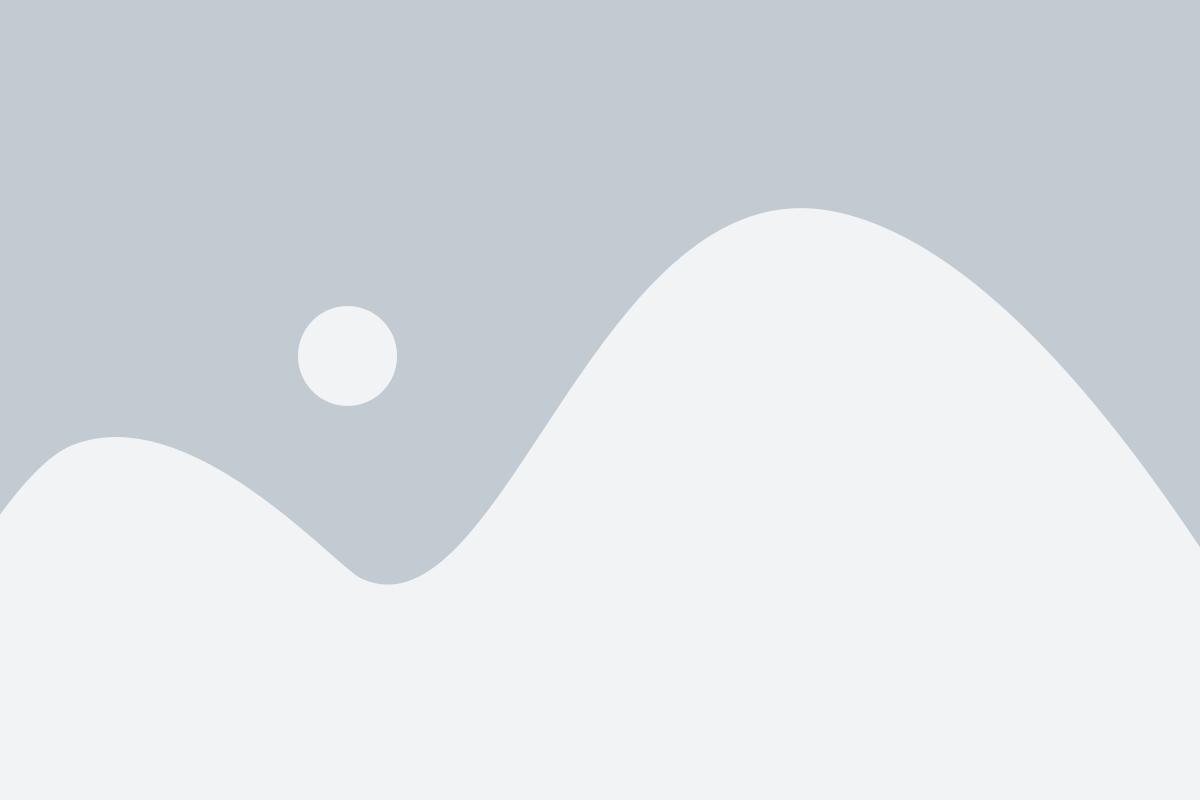
Asset & Work Order Linkage
Tie downtime logs to the specific asset involved — and see which work order followed or triggered the delay.
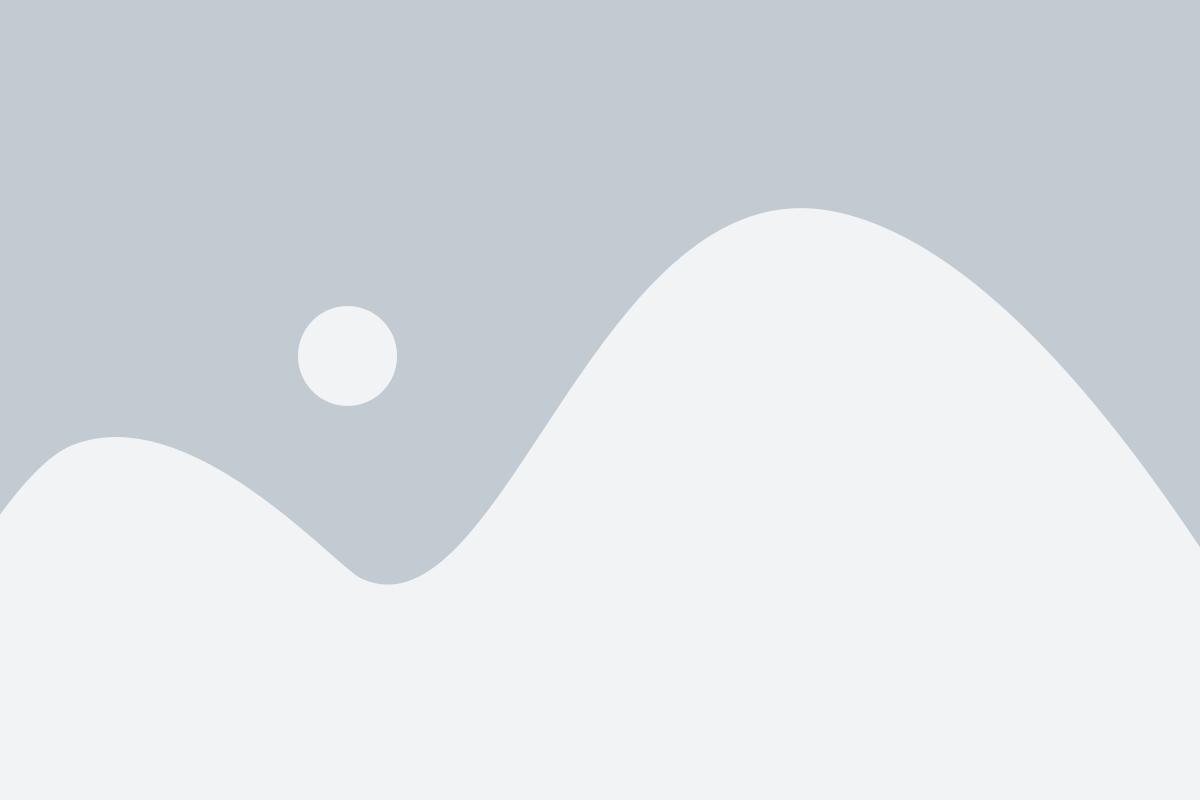
Visual Downtime Calendar View
Get a birds-eye view of downtime events by day, shift, or asset — color-coded by type or severity.
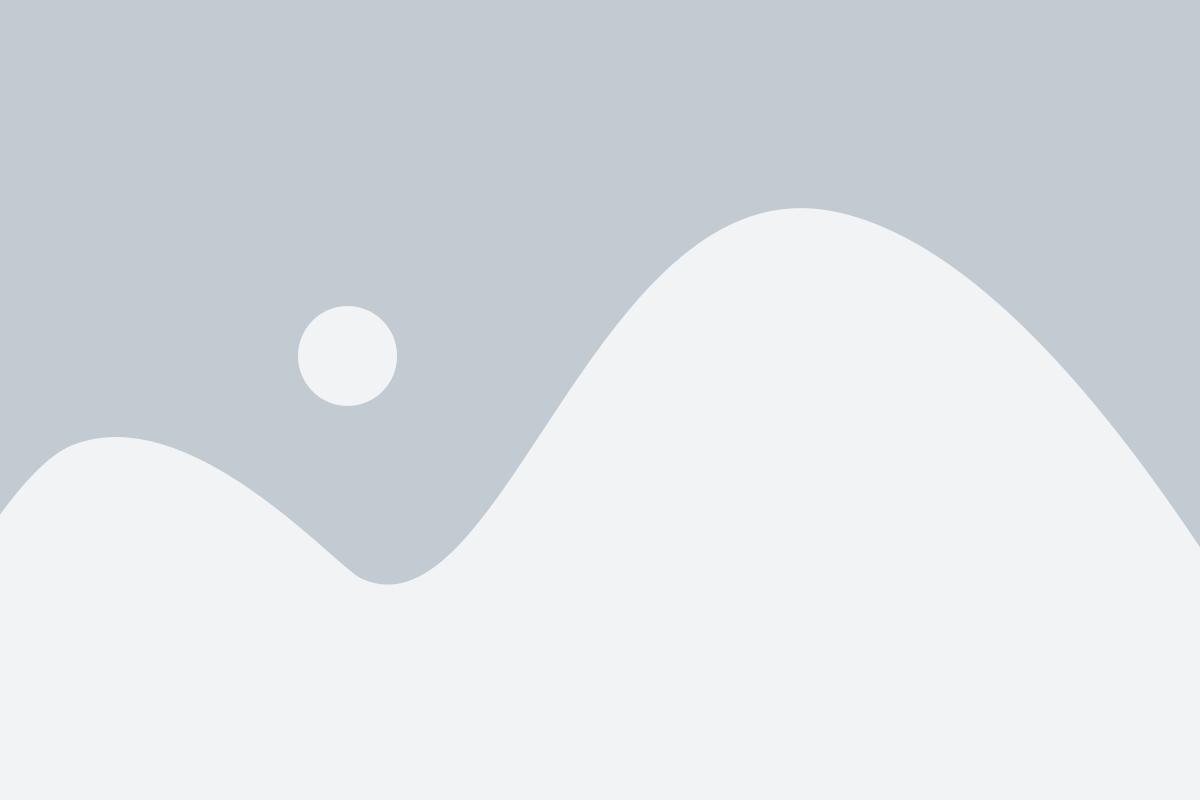
Visual Downtime Calendar View
Get a birds-eye view of downtime events by day, shift, or asset — color-coded by type or severity.
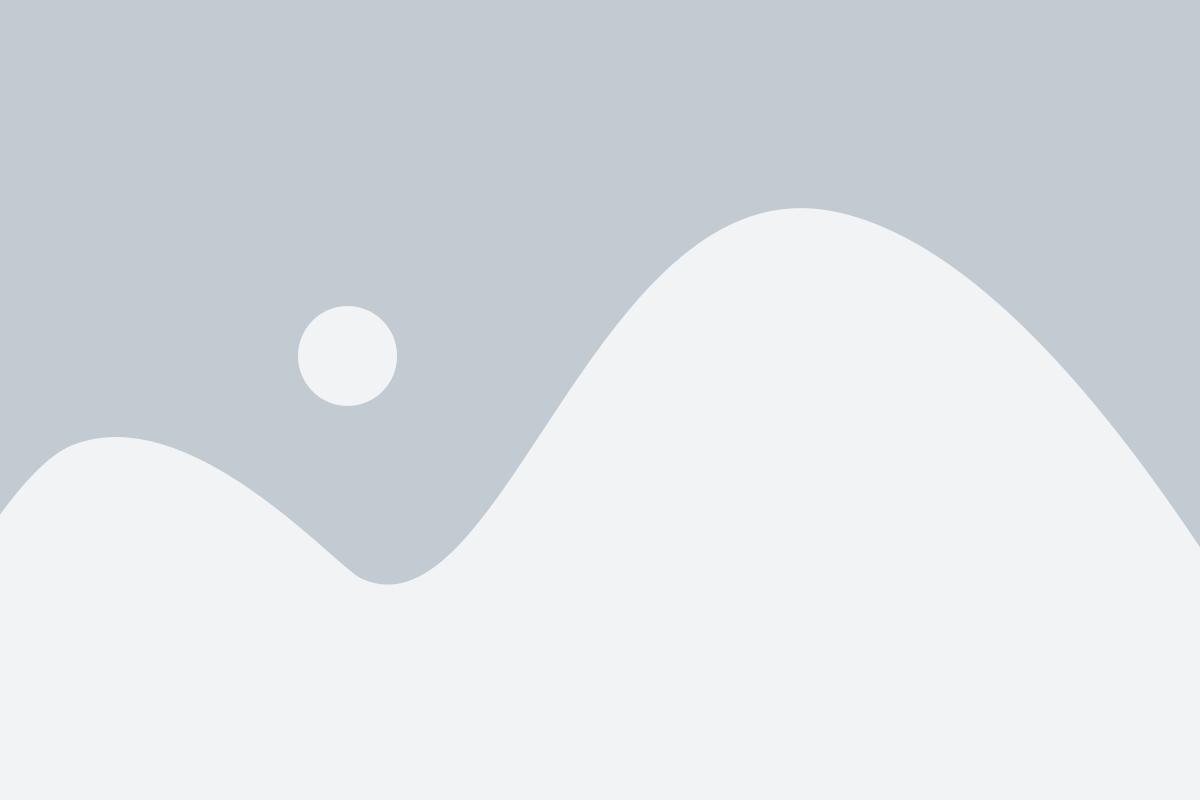
Dashboards & KPI Reporting
Filter downtime by asset, duration, reason, or technician to surface problem areas and drive improvement.
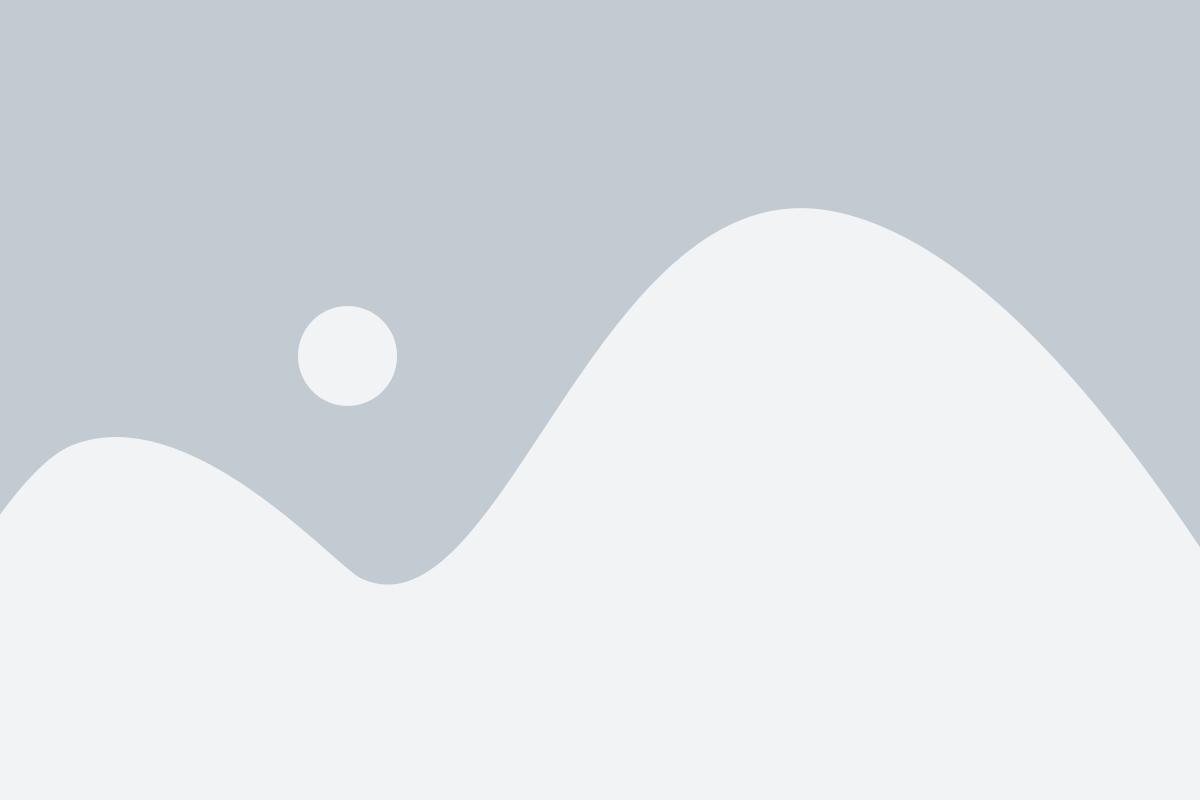
Audit-Ready Export & Event History
All logs are timestamped, traceable, and exportable for audits, compliance, or historical reviews.
See It in Action
Know what stopped, when, and why.
Track every minute of lost time — and use it to power improvements.